Author
Carrera Barbier, Martí
|
Abstract
Modifying the mechanical properties of aluminum alloys is, nowadays, possible by sequential heating and cooling processes in heat treatments, which consist of three stages: solution treatment, quenching and aging.
Thanks to the correlation of the existing physical-metallic properties, improved versions can be obtained by controlling the temperature and time, which are key parameters in a thermal process to cause a microstructural transformation by influencing and altering the size, density and number of grain boundaries that directly affect the movement of dislocations in the aging stage, thus increasing the nominal hardness of the material.
In this work, an investigation is carried out in the analysis of the hardness changes at each stage of the heat treatment for alloyed aluminum samples for the AA6082 T6 alloy with the objective of checking if, subjecting the Al-Mg-Si alloy to different conditions of natural and artificial aging process, it is possible to reverse the T6 aging capacity by means of hardness tests as a study parameter.
For this purpose, a working strategy has been designed consisting of 3 tests whose objective is to compare in which of them better hardness results are obtained at the same tempering and aging conditions, with the difference that, for the second test, natural aging is also carried out at different times.
The tempering conditions are carried out at 520, 540, 560, 580 and 600 ºC with times of approximately 30 minutes and the artificial aging conditions are carried out at 105, 120, 140 and 160 ºC with times of 1, 2, 3 and/or 4 hours depending on the corresponding test.
|
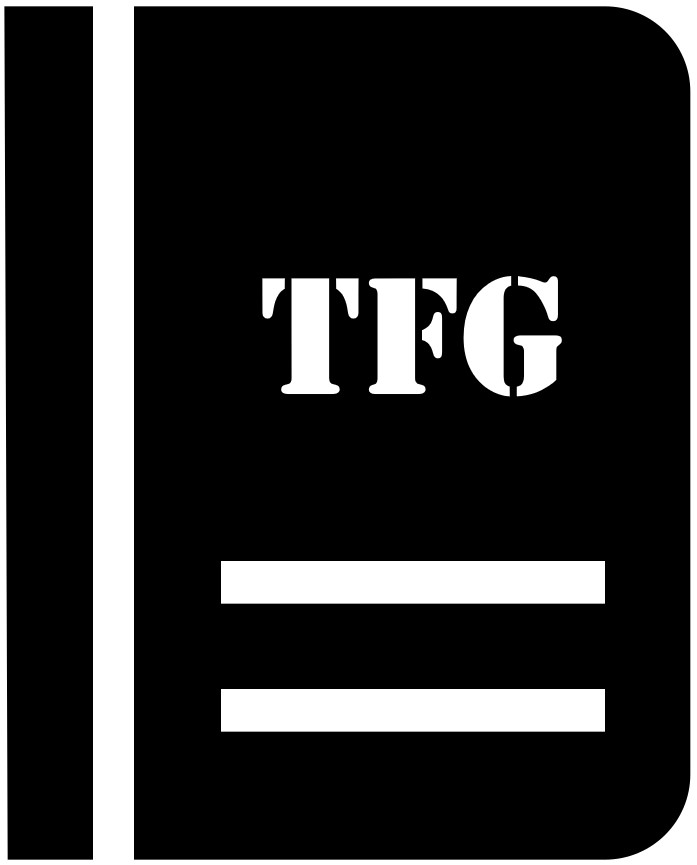
|