Author
Costa Lucero, Marc
|
Today, there are industrial sectors that need real-time monitoring of hydrogen or its isotopes for some processes. These processes take place at very high temperatures, especially in the nuclear sector. Nuclear fusion reactors will presumably use deuterium and tritium as fuel and, since tritium is only found in small traces in nature, it will have to be generated in situ, so it will be necessary to quantify it using devices. For this reason, solid proton conductors are a good alternative for the construction of hydrogen sensors thanks to their chemical stability and ability to work correctly at high temperatures.
In previous studies carried out in the IQS Electrometric Methods laboratory, the ceramic BaCe0,6Zr0,3Y0,1O3-α has been used as an electrolyte for the construction of hydrogen sensors. This ceramic material is a proton conductive oxide that is synthesized in the same laboratory in the form of ceramic powder, being subsequently sintered in the form of a pellet in a furnace.
Currently, sintered tablets give good results but it is possible to increase the proton conductivity to improve the response of the sensors by increasing the densification of the tablet during heat treatment. For this reason, it is proposed to reduce the particle size of the synthesized ceramic pulse on a nanometric scale to favor a better union of the particles and increase the densification of the pellet.
This work explores the flame spray pyrolysis technique, a wet synthesis method that allows the production of nanoparticles. Various methods of collecting the generated particles are explored, as well as improvements to the flame spray pyrolysis equipment are designed and installed. The precursor solution is optimized and nano-sized particles are achieved, but not in the desired quantities, which will have to be improved in future studies.
Finally, to explore other synthesis routes, ceramic pulse particles are synthesized using the glycine method, also wet. The synthesis method, based on the combustion reaction, makes it possible to obtain small particles that, after being heat-treated in a furnace, adopt porous structures with a high surface area.
|
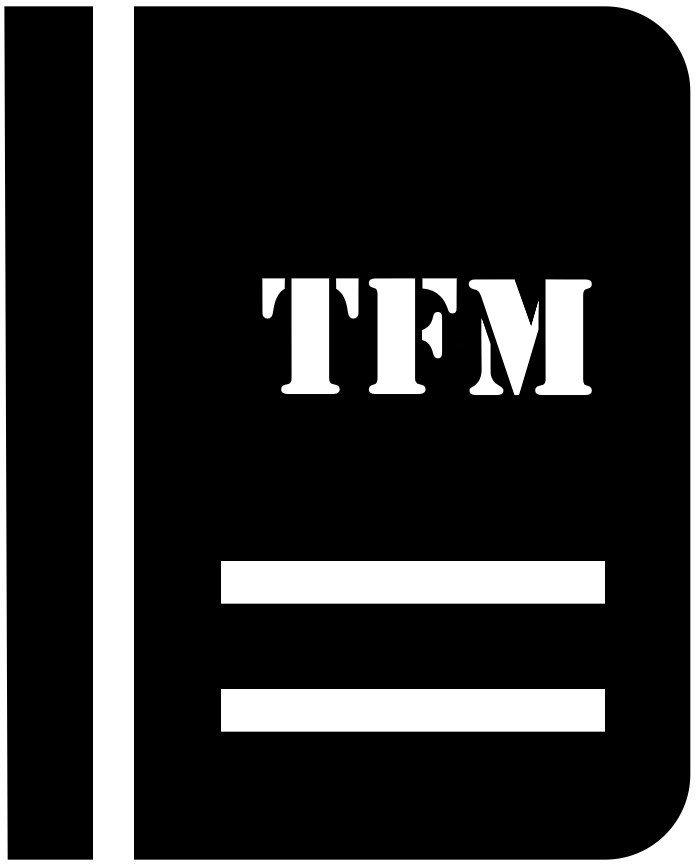
|