Author
Marinel·lo Amat, Alejandro
|
Abstract
The need to look for more specific materials to satisfy human needs forces the industry to find new materials capable of manufacturing them. Materials that offer better mechanical, tribological, and chemical properties are increasingly being sought. Coatings are a method of using the same materials by modifying only the surface of the material. Therefore, it allows using the properties of the substrate material by modifying only the surface to improve the effectiveness of the material.
There are different technologies for depositing coatings on the substrate material. However, one of the most common deposition methods for providing thin layers with excellent mechanical properties is vapor deposition, known as physical vapor deposition (PVD). This technology allows to obtain coatings at low temperatures, so the properties of the substrate material are little altered when subjected to heat treatment. This technique allows achieving coatings with great application in the machining industry, such as CrN, TiN, TiNAl, or DLC.
DLC (Diamond-Like Carbon) coatings are of great importance today because they combine excellent hardness properties and a very low coefficient of friction. These properties are highly sought after in industries. For example, machining elements that reduce friction seek these properties to improve service life and reduce production costs. One of the drawbacks of DLC coatings is that their adhesion is not as good as other coatings. However, it can be improved by applying interlayers that reduce the stress between the DLC and the substrate material.
In this study, the mechanical properties, adherence, and composition of DLC coatings will be analyzed by depositing intermediate layers of chromium and nitrogen and trying not to alter the mechanical properties of the substrate material by performing PVD at low temperature using PVD magneto sputtering and HiPIMS.
|
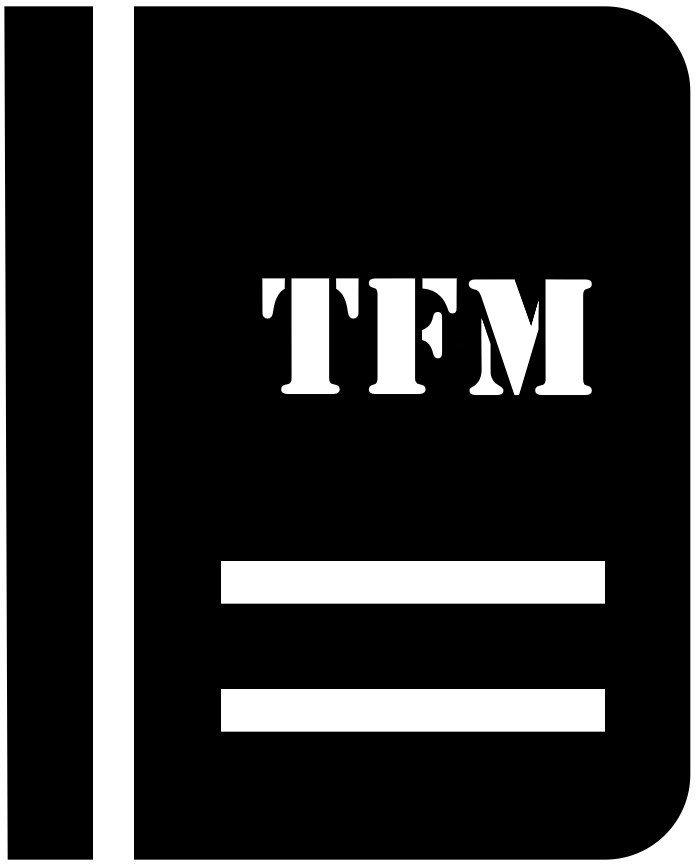
|