Autors/es
Travieso-Rodriguez, J.A., Jerez-Mesa, R.; Llumà, Jordi; Gomez-Gras, Giovanni ; Casadesus, Oriol
|
Abstract
Purpose: The aim of this paper is to analyze the mechanical properties of acrylonitrile-butadiene-styrene (ABS) parts manufactured through fused filament fabrication and compare these results to analogous ones obtained on polylactic acid (PLA) and PLA–wood specimens to contribute for a wider understanding of the different materials used for additive manufacturing. Design/methodology/approach: With that aim, an experimental based on an L27 Taguchi array was used to combine the specific parameters taken into account in the study, namely, layer height, nozzle diameter, infill density, orientation and printing velocity. All samples were subjected to a four-point bending test performed according to the ASTM D6272 standard. Findings: Young’s modulus, elastic limit, maximum stress and maximum deformation of every sample were computed and subjected to an analysis of variance. Results: prove that layer height and nozzle diameter are the most significant factors that affect the mechanical resistance in pieces generated through additive manufacturing and subjected to bending loads, regardless of the material. Practical implications: The best results were obtained by combining a layer height of 0.1 mm and a nozzle diameter of 0.6 mm. The comparison of materials evidenced that PLA and its composite version reinforced with wood particles present more rigidity than ABS, whereas the latter can experience further deflection before break. Originality/value: This study is of interest for manufacturers that want to decide which is the best material to be applied for their application, as it derives in a practical technical recommendation of the best parameters that should be selected to treat the material during the fused filament fabrication process.
|
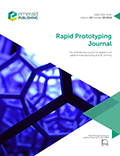
WoS
Scopus
Altmetrics
|
Publicació
Rapid Prototyping Journal, 28 October 2020, v.27, n.1, p.81-92
|